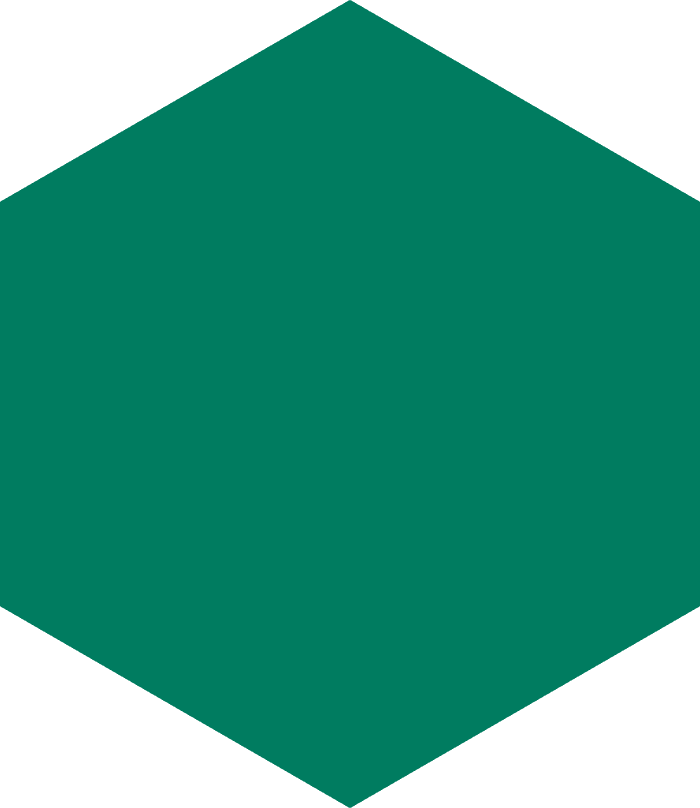
事例紹介CASE
-
どんなに困難な課題であっても、最善の答えを導き出す。
一貫生産体制の強みと柔軟な対応力を活かし、私たちがお客様に貢献し、お喜びいただいた事例をご紹介します。
- 50種類ほどの部品を
約72時間で対応 - 顧客内において試験用の部品の注文漏れが発覚し、新商品の開発スケジュールに影響が出てしまうかもしれないという事態に。そこで当社に、複数種類かつ短期間で生産したいというお話をいただきました。
- 丸秀の対応
- レーザーやプレスブレーキなど汎用的な加工方法を専門とした生産ラインがあるため、事前準備の必要なくすぐに生産を開始。多品種少量の生産管理の実績を活かし、優先順位づけなど行いながら、溶接や塗装まで自社で行うことで約72時間での生産を可能にしました。
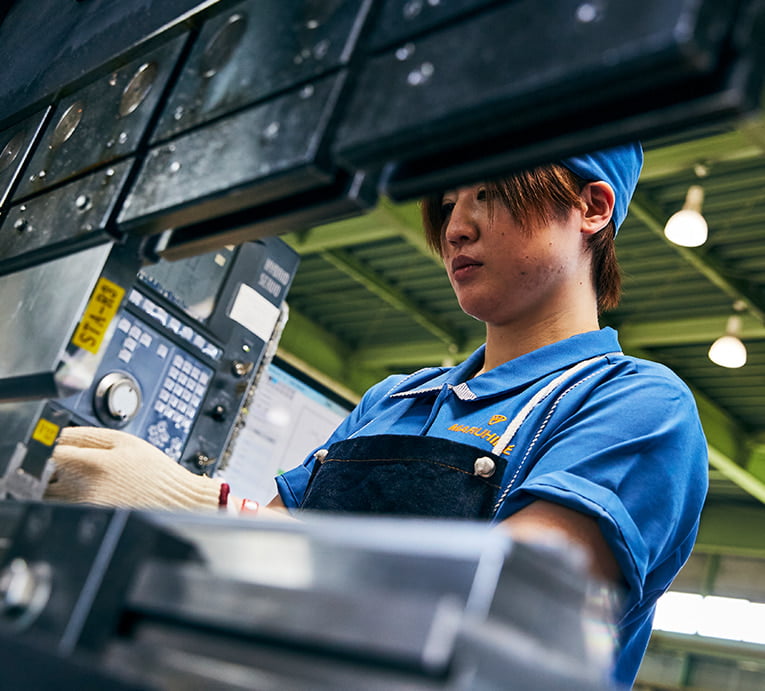
- 既存の金型を改修し、
短期間で設計を変更 -
- 製品のリリース直前に、設計上の不具合が見つかってしまった。その対策として、当社の部品の形状を変更する必要があり、短期間での対応を求められました。
- 丸秀の対応
- お客様のご要望に迅速に応えるため、正式な顧客承認の前から動き出し、金型部材の在庫を活用。金型が内製できることで即座に改修作業に入ることができ、わずか24時間で生産することができました。
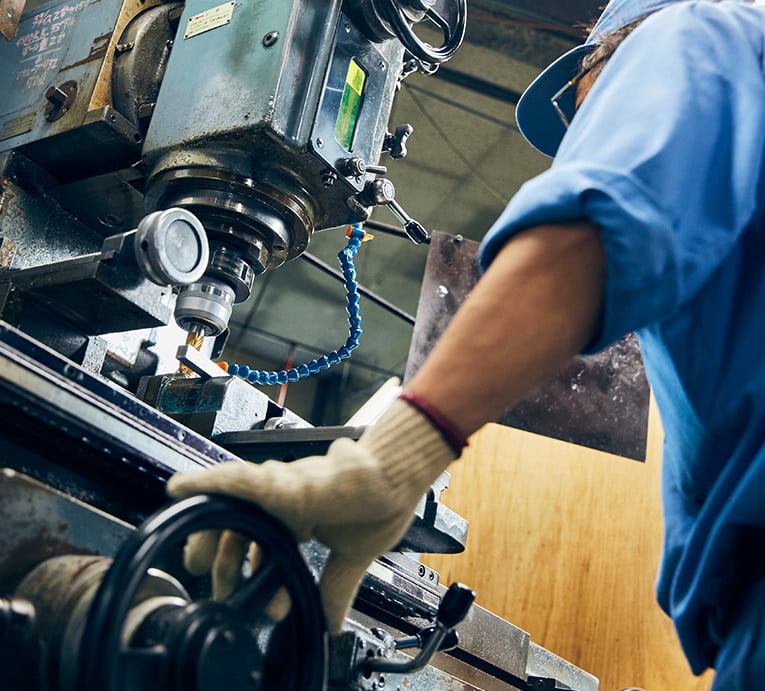
- すべて自動化することで
多品種でも高い管理力を実現 -
- 製造業のお客様より、多品種を発注した際に、納品時に数量不足や品目を間違える会社が多いので、確実に納品してくれる会社を探しているとご相談いただきました。
- 丸秀の対応
- 生産管理機能と入出庫管理機能を連携させ、倉庫業務をすべて自動化。また、製品1個あたりの重量を管理するシステムを自社開発し、少量から大量まですべての重量管理に成功。これらの徹底した管理により、確実な納品を実現させることができました。現在は日々3,000品目を出荷管理しています。
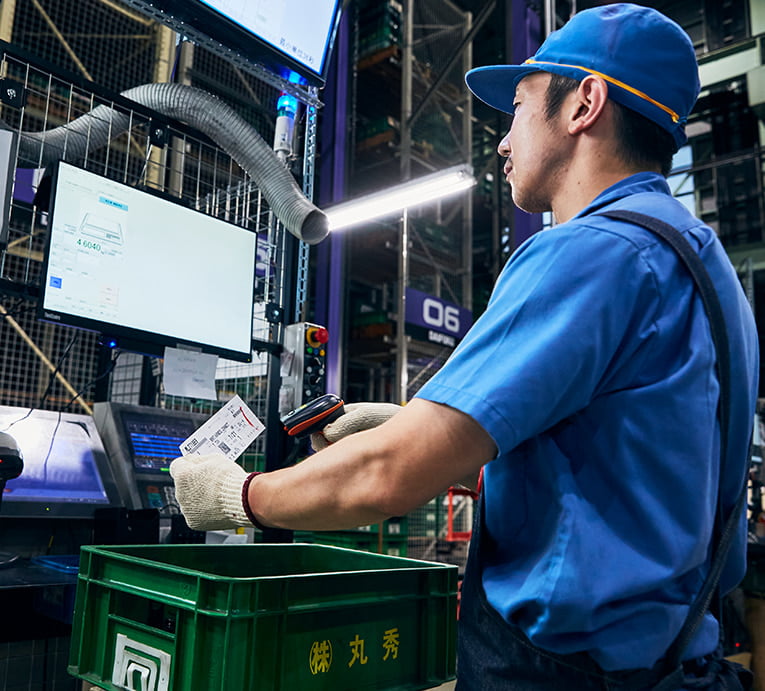
- Q.D.C金型により
中量製品のコストを最適化 -
- 車両製造業の企業様より、月間所要量が50~300個程度のため大手では非効率になると対応してもらえず、自社の予算も満たしてくれる会社が見つからないとご相談いただきました。
- 丸秀の対応
- 少量用工法「レーザー+プレスブレーキ」と中量用工法「Q.D.C金型を用いたプレス加工」を組み合わせたハイブリッドで生産に対応。一部のみ金型を作ることで、コストを抑えることもできました。
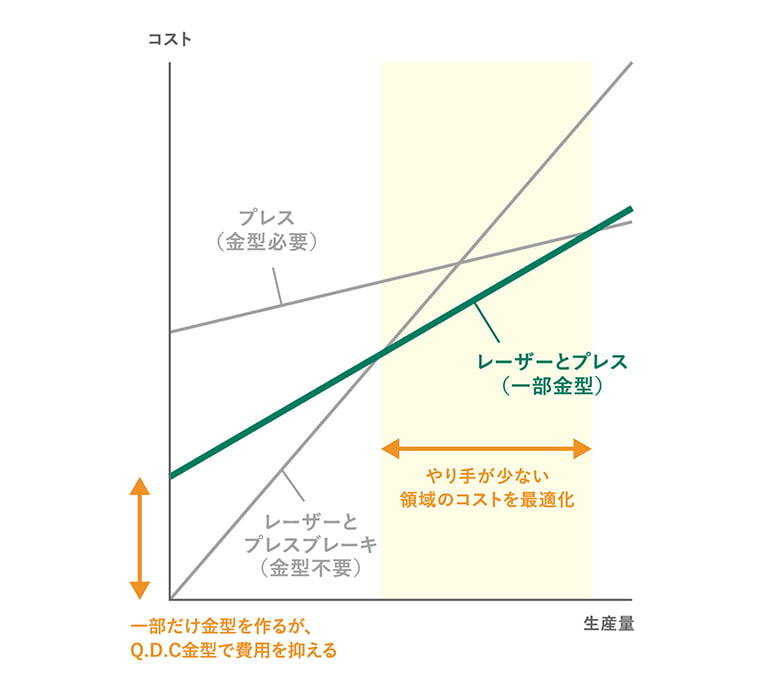
- 特殊事例紹介
- 丸秀では、生産が高難度な製品を、
大量かつ安定して供給することに特化した
一貫生産体制も整えています。
製作難度が高い製品に対し、
生産性と高品質を両立
(オイルシールメーカー様)
オイルシールは、5/100ミリの寸法精度、難形状、要求仕様など製作難度が高く、技術力や対応力が求められます。丸秀では、機械加工精度を確保する特殊なプレス機とNC旋盤による加工を行うとともに、生産性向上と高品質を両立させるため以下の対応を行っています。
- 供給体制 1,000トン・600トンプレスを擁し、特殊な製品仕様にあった供給体制が整っている。1,000トンプレスでありながら、材料幅600ミリまでとした特殊仕様で難形状に対応しています。
- コスト対応 段取替え(金型交換)を迅速に行うムービングボルスターにより、移動距離が最短となる仕様にすることでコスト面に対応。また、少品種大量という特性に対応するため、箱詰め・自動旋盤・バリ取りの自動化を進行しています。
- 品質管理 誰が、どの材料を、どのような方法で、いつ加工したかを記録し、トレーサビリティに対応。品質面で異常があった場合は2時間以内で回答できます。また、改修もすぐに対応できるよう、自社で金型メンテナンスも行っています。